We want to share with you the story of CIA – ABOLIV,
to show you the most important moments in our evolution:
1992
The CIA ABOLIV company comes to life. The 500 kg of deli meats, produced daily by the fresh factory, were sold in a small area, near Turda - Câmpia Turzii. Two stores were opened. At that time, the production section was equipped with Romanian equipment (choppers, cutter, mixer), while using traditional boiling andsmoking techniques. The CIA-ABOLIV family had 20 members.1996/1997
Our products were very popular, increasing the demand. Thus, we decided to build a new factory, of around 1000m². Modern equipment has been purchased from major global manufacturers in the field. From this point, due to the modernization on the technological flow, the production gradually registered a dynamic of constant growth, but also a diversification of the assortments.2004
This was a very important year in our journey, because it was the moment when we entered the modern market and we started to collaborate with the big retailers, to produce deli meats for the big stores. This determined us to take a step on generating a big development and expansion.2005
Romania was in the period of pre-accession to the European Union, and the support programs motivated us and offered us the possibility to access funds for the construction of a new modern factory, in accordance with the requirements and norms of the EU. Thus, with the help of the SAPARD program, we started to build today's CIA-ABOLIV factory, which was to have a production capacity of 20 tons per day.2006
Work on the new meat factory has been completed. CIA-ABOLIV thus becameone of the first deli meats factories in Romania with a technological flow in accordance with European norms. The production capacity exceeded 20 tons per day, and we managed to offer new jobs, due to the newly made investments. The technological line has been improved, we have purchased new state-of-the-artequipment in the meat industry, which considerably improved the quality of the products, by strictly monitoring the traceability in the production process. The total investment was about 4.5 million euros.2007
We implemented HACCP (Hazard Analysis and Critical Control Points) and ISO 9001-2000 systems. Besides,this year we obtained the sanitary veterinary authorization for intra-community exchanges.2009
YEAR OF DEVELOPMENT. By 2009 we managed to grow considerably,and we ended up producing about 40 tons of deli meats daily. Our factory has reached a number of 250 employees. Out of our desire for continuous improvement, this year we implemented the ISO 22000 - 2005 Food Safety Management System.This improvement had a significant impact on the company's development. Our credibility has increased and the fact that we have implemented the highest standards in the field has made us become important players in the market. The quality and safety of our products now became difficult to match.2011
We continued the modernization process, and in the first part of 2011 a modern slaughter house unit was put into use, which met the highest requirements imposed by European legislation. We have always put a special emphasis on the raw material, choosing our suppliers very carefully, and this investment has helped ensure a larger quantity of fresh meat for stores and limited our need to import. The costs amounted to about 1 millioneuros.2013
We have built and inaugurated a logistics warehouse for the storage of finished products, where state-of-the-art techniques were used for handling, sorting and packaging products. The ware house had a capacity of 180 tons. The use of WMS (Warehouse Management Systems) is an asset, allowing us to control the movement of products in warehouses through a computer system. The most important benefits of using this system are: inventory optimization, organization of storage space, rapid inventory, picking activities, trace ability of products from reception to exit from the warehouse.2014
We have built a freezer warehouse with a capacity of 400 tons, which held and assured we had the necessary raw material for a reasonable period of time. We inaugurated a modern presentation store located in the Central Square of Turda.2015
We have inaugurated a special spice warehouse, which ensured we had the necessary spices for a reasonable period of time. Also this year we implemented the Standard for Food Quality and Safety Assurance "INTERNATIONAL FOOD STANDARDS" (IFS), obtaining the "HigherLevel"score. In 2015, 2 modern presentation stores were inaugurated in Câmpia Turzii and in Turda,near Materna.2016
We have built and inaugurated a packaging / thermoforming warehouse, where everything is automated, with state-of-the-artmachines, which ensure packaging in conditions of maximum hygiene and safety. Another modern presentation store was inaugurated in Mihai Viteazu commune.2019
A new modern presentation store was opened in Floresti.2020
Was inaugurated the ripening hall for raw-dried products, at the highest standards, with a capacity of 55 tons. We have built a freezing warehouse with a capacity of 580 tons, which ensures the raw material requirement for a reasonable period of time.2022
We have inaugurated the ripening, slicing and packaging hall:It has an area of 1094 m2, a raw-dry ripening capacity of 29 tons/week and a slicing and packing capacity of 5 tons/day. The value of the investment amounts to 3.5 million euros. The department is equipped with state-of-the-art machines in the field of sliced products.
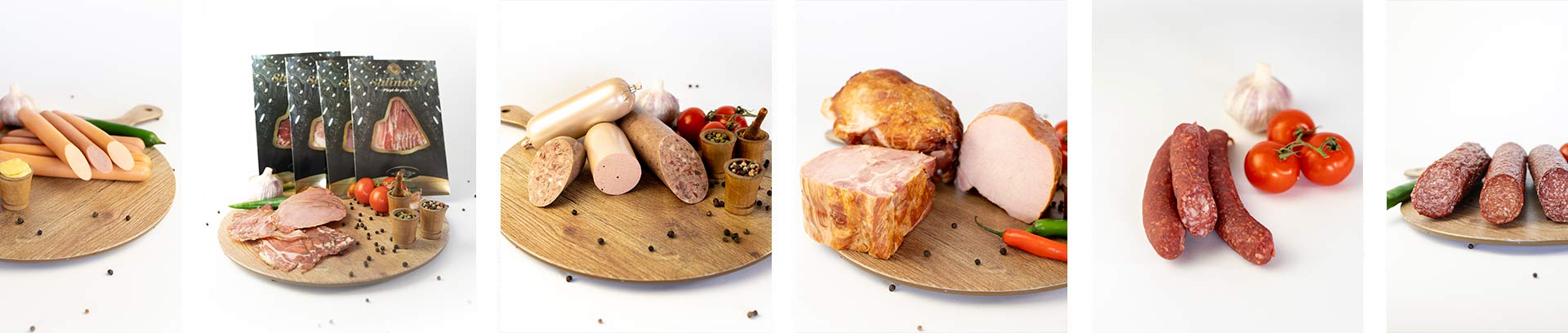